Az SPC (statisztikai folyamatirányítás) kulcsfontosságú eszköz a wafer gyártási folyamatában, amelyet a gyártás különböző szakaszainak stabilitásának monitorozására, szabályozására és javítására használnak.
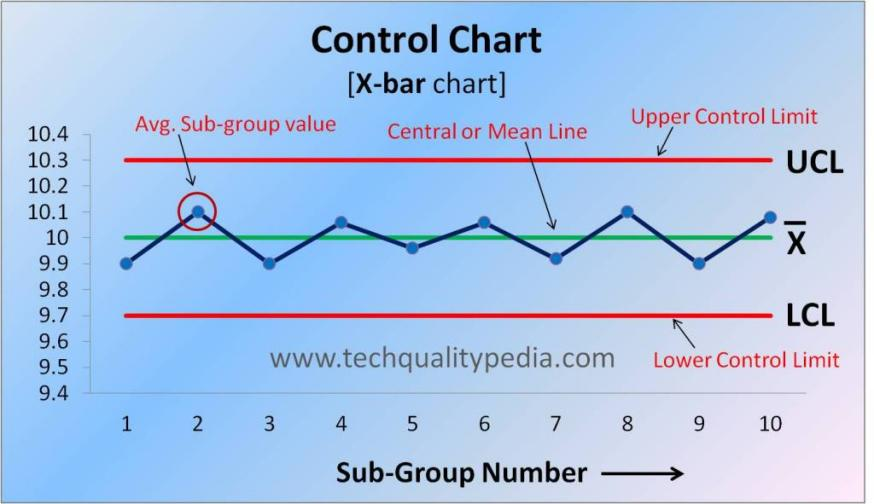
1. Az SPC rendszer áttekintése
Az SPC egy olyan módszer, amely statisztikai technikákat alkalmaz a gyártási folyamatok monitorozására és szabályozására. Fő funkciója a gyártási folyamatban előforduló rendellenességek észlelése valós idejű adatok gyűjtése és elemzése révén, segítve a mérnököket az időben történő kiigazításokban és döntések meghozatalában. Az SPC célja a gyártási folyamat eltéréseinek csökkentése, biztosítva a termékminőség stabilitását és a specifikációknak való megfelelést.
Az SPC-t a maratási folyamatban a következőkre használják:
A kritikus berendezésparaméterek monitorozása (pl. maratási sebesség, rádiófrekvenciás teljesítmény, kamranyomás, hőmérséklet stb.)
Elemezze a legfontosabb termékminőségi mutatókat (pl. vonalszélesség, maratási mélység, él érdessége stb.)
Ezen paraméterek monitorozásával a mérnökök képesek észlelni a berendezések teljesítményének romlására vagy a gyártási folyamat eltéréseire utaló trendeket, ezáltal csökkentve a selejtarányokat.
2. Az SPC rendszer alapvető összetevői
Az SPC rendszer több kulcsfontosságú modulból áll:
Adatgyűjtő modul: Valós idejű adatokat gyűjt a berendezésekről és a folyamatokról (pl. FDC, EES rendszereken keresztül), és rögzíti a fontos paramétereket és a termelési eredményeket.
Szabályozódiagram modul: Statisztikai szabályozási diagramokat (pl. X-sávdiagram, R-diagram, Cp/Cpk-diagram) használ a folyamat stabilitásának vizualizálására és annak meghatározására, hogy a folyamat kontroll alatt van-e.
Riasztórendszer: Riasztást vált ki, ha a kritikus paraméterek túllépik a szabályozási határértékeket vagy trendváltozásokat mutatnak, ami arra ösztönzi a mérnököket, hogy intézkedjenek.
Elemző és jelentéskészítő modul: Az SPC-diagramok alapján elemzi az anomáliák kiváltó okát, és rendszeresen teljesítményjelentéseket készít a folyamatokról és a berendezésekről.
3. Az SPC-ben található vezérlőkártyák részletes magyarázata
A szabályozási diagramok az egyik leggyakrabban használt eszköz az SPC-ben, amelyek segítenek megkülönböztetni a „normális eltérést” (amelyet a természetes folyamatváltozások okoznak) és az „abnormális eltérést” (amelyet a berendezés meghibásodása vagy a folyamat eltérései okoznak). A gyakori szabályozási diagramok a következők:
X-Bar és R diagramok: A gyártási tételeken belüli átlag és tartomány monitorozására szolgálnak, hogy megfigyelhető legyen a folyamat stabilitása.
Cp és Cpk indexek: A folyamatképesség mérésére szolgálnak, azaz hogy a folyamat kimenete következetesen megfelel-e a specifikációs követelményeknek. A Cp a potenciális képességet méri, míg a Cpk a folyamatközéppont eltérését veszi figyelembe a specifikációs határoktól.
Például a maratási folyamat során olyan paramétereket figyelhet, mint a marási sebesség és a felületi érdesség. Ha egy adott berendezés marási sebessége meghaladja a szabályozási határértéket, vezérlőkártyák segítségével meghatározhatja, hogy ez természetes változás-e, vagy a berendezés meghibásodásának jele.
4. SPC alkalmazása maratógépekben
A maratási folyamat során a berendezés paramétereinek szabályozása kritikus fontosságú, és az SPC a következő módokon segít javítani a folyamat stabilitását:
Berendezések állapotfelügyelete: Az olyan rendszerek, mint az FDC, valós idejű adatokat gyűjtenek a maratóberendezések kulcsfontosságú paramétereiről (pl. RF teljesítmény, gázáramlás), és ezeket az adatokat kombinálják az SPC vezérlődiagramjaival a potenciális berendezésproblémák észlelése érdekében. Például, ha azt látja, hogy a vezérlődiagramon az RF teljesítmény fokozatosan eltér a beállított értéktől, korai intézkedéseket hozhat a beállítás vagy a karbantartás érdekében, hogy elkerülje a termékminőség befolyásolását.
Termékminőség-felügyelet: A kulcsfontosságú termékminőségi paramétereket (pl. maratási mélység, vonalszélesség) is megadhatja az SPC rendszerben, hogy figyelemmel kísérhesse azok stabilitását. Ha egyes kritikus termékmutatók fokozatosan eltérnek a célértékektől, az SPC rendszer riasztást ad, jelezve, hogy folyamatmódosításokra van szükség.
Megelőző karbantartás (PM): Az SPC segíthet optimalizálni a berendezések megelőző karbantartási ciklusát. A berendezések teljesítményére és a folyamateredményekre vonatkozó hosszú távú adatok elemzésével meghatározható a berendezés karbantartásának optimális időpontja. Például az RF teljesítmény és az ESC élettartamának figyelésével meghatározható, hogy mikor van szükség tisztításra vagy alkatrészcserére, csökkentve a berendezések meghibásodási arányát és a termelési állásidőt.
5. Tippek az SPC rendszer napi használatához
Az SPC rendszer napi működés közbeni használatakor a következő lépéseket kell követni:
Kulcsfontosságú szabályozási paraméterek (KPI) meghatározása: A termelési folyamat legfontosabb paramétereinek azonosítása és az SPC-monitorozásba való beépítése. Ezeknek a paramétereknek szorosan kapcsolódniuk kell a termékminőséghez és a berendezések teljesítményéhez.
Szabályozási és riasztási határértékek beállítása: A korábbi adatok és a folyamatkövetelmények alapján állítson be ésszerű szabályozási és riasztási határértékeket minden paraméterhez. A szabályozási határértékek általában ±3σ-ra (szórás) vannak beállítva, míg a riasztási határértékek a folyamat és a berendezés sajátos körülményein alapulnak.
Folyamatos monitorozás és elemzés: Az SPC vezérlődiagramjait rendszeresen felül kell vizsgálni az adattrendek és -változások elemzése érdekében. Ha egyes paraméterek meghaladják a szabályozási határértékeket, azonnali beavatkozásra van szükség, például a berendezés paramétereinek módosítására vagy a berendezés karbantartására.
Rendellenesség kezelése és ok-ok elemzése: Rendellenesség esetén az SPC rendszer részletes információkat rögzít az incidensről. Ezen információk alapján kell elhárítani a hibát és elemezni a rendellenesség okát. Gyakran lehetőség van az FDC rendszerekből, EES rendszerekből stb. származó adatok kombinálására annak elemzésére, hogy a probléma berendezéshibára, folyamateltérésre vagy külső környezeti tényezőkre vezethető vissza.
Folyamatos fejlesztés: Az SPC rendszer által rögzített historikus adatok felhasználásával azonosítsa a folyamat gyenge pontjait, és javasoljon fejlesztési terveket. Például a maratási folyamatban elemezze az elektronikus szabályzók (ESC) élettartamának és tisztítási módszereinek hatását a berendezések karbantartási ciklusaira, és folyamatosan optimalizálja a berendezések működési paramétereit.
6. Gyakorlati alkalmazási eset
Gyakorlati példaként tegyük fel, hogy Ön felelős az E-MAX maróberendezésért, és a kamra katódja idő előtti kopást tapasztal, ami a D0 (BARC hiba) értékek növekedéséhez vezet. Az RF teljesítmény és a marási sebesség SPC rendszeren keresztüli monitorozásával azt a trendet veszi észre, hogy ezek a paraméterek fokozatosan eltérnek a beállított értékektől. Miután egy SPC riasztás kioldódik, az FDC rendszerből származó adatokat kombinálva megállapítja, hogy a problémát a kamrán belüli instabil hőmérséklet-szabályozás okozza. Ezután új tisztítási módszereket és karbantartási stratégiákat vezet be, amelyek végül 4,3-ról 2,4-re csökkentik a D0 értéket, ezáltal javítva a termék minőségét.
7. A XINKEHUI-ban szerezhetsz.
A XINKEHUI-nál megtalálhatja a tökéletes ostyát, legyen szó szilícium- vagy SiC-ostyáról. Szakterületünk a kiváló minőségű ostyák szállítása különböző iparágak számára, a pontosságra és a teljesítményre összpontosítva.
(szilícium ostya)
Szilíciumlapkáink kiváló tisztasággal és egyenletességgel készülnek, biztosítva a félvezetői igényeinek kiváló elektromos tulajdonságait.
Az igényesebb alkalmazásokhoz SiC ostyáink kivételes hővezető képességet és nagyobb energiahatékonyságot kínálnak, így ideálisak teljesítményelektronikához és magas hőmérsékletű környezetekhez.
(SiC ostya)
A XINKEHUI-val élvonalbeli technológiát és megbízható támogatást kap, garantálva a legmagasabb iparági szabványoknak megfelelő wafereket. Válasszon minket a tökéletes waferért!
Közzététel ideje: 2024. október 16.