A félvezetőgyártási folyamat kritikus lépéseként a wafer kockázási technológia közvetlenül összefügg a chip teljesítményével, hozamával és gyártási költségeivel.
#01 Az ostyaszeletelés háttere és jelentősége
1.1 Az ostyakockázás definíciója
A wafer kockázás (más néven karcolás) a félvezetőgyártás egyik alapvető lépése, amelynek célja a feldolgozott waferek több különálló chipre osztása. Ezek a chipek jellemzően teljes áramköri funkciókat tartalmaznak, és végső soron az elektronikus eszközök gyártásának fő alkotóelemei. Ahogy a chipek kialakítása egyre összetettebbé válik, és a méretek folyamatosan csökkennek, a wafer kockázási technológiával szembeni pontossági és hatékonysági követelmények egyre szigorúbbak.
A gyakorlatban az ostyaaprítás jellemzően nagy precíziós szerszámokat, például gyémántlapokat használ, hogy biztosítsa minden egyes szerszám épségét és teljes funkcionalitását. A kulcsfontosságú lépések közé tartozik a vágás előtti előkészítés, a precíz ellenőrzés a vágási folyamat során és a vágás utáni minőségellenőrzés.
Vágás előtt a lapkát meg kell jelölni és el kell helyezni a pontos vágási útvonalak biztosítása érdekében. A vágás során az olyan paramétereket, mint a szerszámnyomás és a sebesség, szigorúan ellenőrizni kell, hogy elkerüljük a lapka károsodását. A vágás után átfogó minőségellenőrzéseket végeznek annak biztosítására, hogy minden chip megfeleljen a teljesítménykövetelményeknek.
A szeletvágási technológia alapelvei nemcsak a vágóberendezések kiválasztását és a folyamatparaméterek beállítását foglalják magukban, hanem az anyagok mechanikai tulajdonságainak és jellemzőinek a vágási minőségre gyakorolt hatását is. Például az alacsony k dielektromos szilícium szeletek gyengébb mechanikai tulajdonságaik miatt nagyon érzékenyek a feszültségkoncentrációra a vágás során, ami olyan hibákhoz vezet, mint a lepattogzás és a repedés. Az alacsony k anyagok alacsony keménysége és ridegsége miatt hajlamosabbak a szerkezeti károsodásra mechanikai erő vagy hőfeszültség alatt, különösen vágás közben. A szerszám és a szelet felülete közötti érintkezés, a magas hőmérséklettel párosulva, tovább súlyosbíthatja a feszültségkoncentrációt.
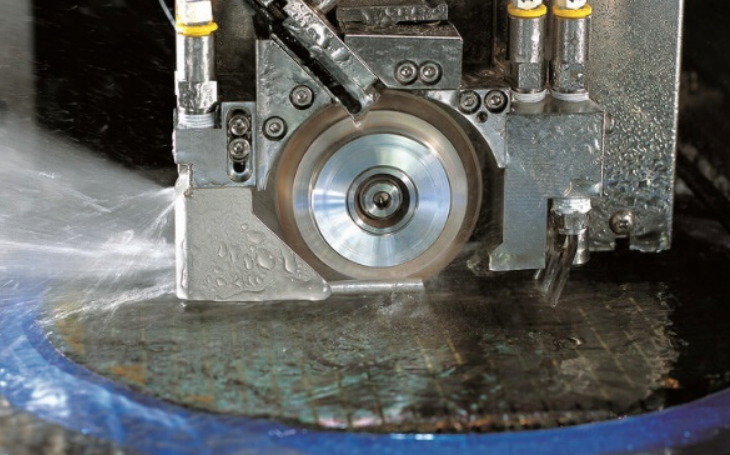
Az anyagtudomány fejlődésével a szeletvágási technológia túlmutat a hagyományos szilíciumalapú félvezetőkön, és olyan új anyagokat is magában foglal, mint a gallium-nitrid (GaN). Ezek az új anyagok keménységük és szerkezeti tulajdonságaik miatt új kihívásokat jelentenek a vágási folyamatok számára, ami további fejlesztéseket igényel a forgácsolószerszámokban és technikákban.
A félvezetőiparban kritikus folyamatként a wafer kockázás folyamatosan optimalizálódik a változó igényekre és a technológiai fejlődésre reagálva, megalapozva a jövő mikroelektronikai és integrált áramköri technológiáit.
A wafer aprítási technológia fejlesztései túlmutatnak a segédanyagok és eszközök fejlesztésén. Magukban foglalják a folyamatok optimalizálását, a berendezések teljesítményének javítását és a vágási paraméterek pontos szabályozását is. Ezek a fejlesztések a wafer aprítási folyamat nagy pontosságát, hatékonyságát és stabilitását célozzák, kielégítve a félvezetőipar kisebb méretek, nagyobb integráció és összetettebb chipszerkezetek iránti igényeit.
fejlesztési terület | Konkrét intézkedések | Hatások |
Folyamatoptimalizálás | - A kezdeti előkészületek javítása, például a pontosabb szeletpozicionálás és útvonaltervezés. | - Csökkenti a vágási hibákat és javítja a stabilitást. |
- Minimalizálja a vágási hibákat és fokozza a stabilitást. | - Valós idejű figyelési és visszacsatolási mechanizmusok alkalmazása a szerszámnyomás, -sebesség és -hőmérséklet beállításához. | |
- Alacsonyabb ostyatörési arány és jobb chipminőség. | ||
Berendezések teljesítményének növelése | - Nagy pontosságú mechanikus rendszereket és fejlett automatizálási vezérlési technológiát alkalmaz. | - Növeli a vágási pontosságot és csökkenti az anyagpazarlást. |
- Nagy keménységű anyagú ostyákhoz alkalmas lézervágási technológia bevezetése. | - Növelni a termelési hatékonyságot és csökkenteni a manuális hibákat. | |
- Növelje a berendezések automatizálását az automatikus felügyelet és beállítás érdekében. | ||
Precíz paramétervezérlés | - Finombeállítás olyan paraméterekhez, mint a vágási mélység, a sebesség, a szerszámtípus és a hűtési módszerek. | - Biztosítsa a szerszám integritását és elektromos teljesítményét. |
- Testreszabhatja a paramétereket az ostya anyaga, vastagsága és szerkezete alapján. | - Növelje a hozamokat, csökkentse az anyagpazarlást és a termelési költségeket. | |
Stratégiai jelentőség | - Folyamatosan új technológiai megoldásokat keresünk, optimalizáljuk a folyamatokat és fejlesztjük a berendezéseinket a piaci igények kielégítése érdekében. | - A chipgyártás hozamának és teljesítményének javítása, új anyagok és fejlett chiptervek fejlesztésének támogatása. |
1.2 Az ostyakockázás fontossága
A szeletek felaprítása kritikus szerepet játszik a félvezetőgyártási folyamatban, közvetlenül befolyásolja a későbbi lépéseket, valamint a végtermék minőségét és teljesítményét. Fontosságát a következőképpen lehet részletezni:
Először is, a kockázás pontossága és következetessége kulcsfontosságú a chipek hozamának és megbízhatóságának biztosításához. A gyártás során a lapkák több feldolgozási lépésen mennek keresztül, hogy számos bonyolult áramköri struktúrát hozzanak létre, amelyeket pontosan különálló chipekre (szerszámokra) kell osztani. Ha a kockázási folyamat során jelentős hibák vannak az igazításban vagy a vágásban, az áramkörök megsérülhetnek, ami befolyásolja a chip működését és megbízhatóságát. Ezért a nagy pontosságú kockázási technológia nemcsak az egyes chipek integritását biztosítja, hanem megakadályozza a belső áramkörök károsodását is, javítva az általános hozamot.
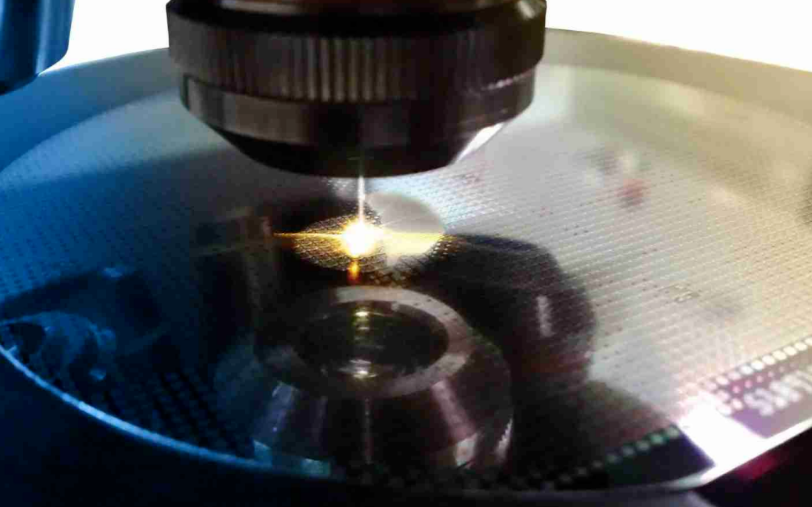
Másodszor, az ostyaaprítás jelentős hatással van a termelési hatékonyságra és a költségellenőrzésre. A gyártási folyamat kulcsfontosságú lépéseként hatékonysága közvetlenül befolyásolja a következő lépések előrehaladását. A aprítási folyamat optimalizálásával, az automatizálási szint növelésével és a vágási sebesség javításával az általános termelési hatékonyság jelentősen javítható.
Másrészt az anyagpazarlás a kockázás során kritikus tényező a költséggazdálkodásban. A fejlett kockázási technológiák alkalmazása nemcsak a vágási folyamat során fellépő felesleges anyagveszteséget csökkenti, hanem növeli a lapkakihasználást is, ezáltal csökkentve a termelési költségeket.
A félvezető technológia fejlődésével a szeletek átmérője folyamatosan növekszik, és az áramköri sűrűség is ennek megfelelően emelkedik, ami nagyobb igényeket támaszt a kockázási technológiával szemben. A nagyobb szeleteknél pontosabb vágási útvonalvezérlésre van szükség, különösen a nagy sűrűségű áramköri területeken, ahol már a kis eltérések is több chipet hibássá tehetnek. Ezenkívül a nagyobb szeletek több vágási vonalat és összetettebb folyamatlépéseket igényelnek, ami további fejlesztéseket tesz szükségessé a kockázási technológiák pontosságában, következetességében és hatékonyságában, hogy megfeleljenek ezeknek a kihívásoknak.
1.3 Ostyakockázási folyamat
Az ostyakockázási folyamat az előkészítési fázistól a végső minőségellenőrzésig minden lépést magában foglal, és minden szakasz kritikus fontosságú a kockára vágott chipek minőségének és teljesítményének biztosítása szempontjából. Az alábbiakban részletesen ismertetjük az egyes fázisokat.
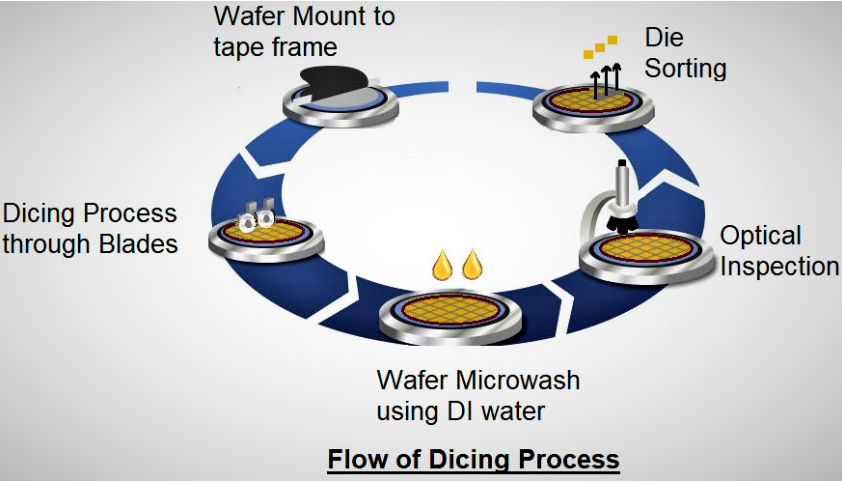
Fázis | Részletes leírás |
Előkészítési fázis | -Ostya tisztításHasználjon nagy tisztaságú vizet és speciális tisztítószereket, ultrahangos vagy mechanikus súrolással kombinálva a szennyeződések, részecskék és szennyeződések eltávolításához, biztosítva a tiszta felületet. -Pontos pozicionálásNagy pontosságú berendezéseket kell használni annak biztosítására, hogy az ostya pontosan fel legyen osztva a tervezett vágási útvonalak mentén. -OstyarögzítésRögzítse a lapkát egy szalagkeretre a vágás közbeni stabilitás megőrzése érdekében, megakadályozva a rezgés vagy mozgás okozta károsodást. |
Vágási fázis | -Penge aprításNagy sebességű, forgó, gyémántbevonatú pengéket használjon fizikai vágáshoz, alkalmas szilícium alapú anyagokhoz és költséghatékony. -Lézeres kockázásNagy energiájú lézersugarakat használjon érintésmentes vágáshoz, ideális törékeny vagy nagy keménységű anyagokhoz, például gallium-nitridhez, nagyobb pontosságot és kisebb anyagveszteséget biztosítva. -Új technológiákLézer- és plazmavágási technológiák bevezetése a hatékonyság és a pontosság további javítása, valamint a hőhatásövezetek minimalizálása érdekében. |
Tisztítási fázis | - Használjon ioncserélt vizet (DI vizet) és speciális tisztítószereket, ultrahangos vagy szórófejes tisztítással kombinálva a vágás során keletkező törmelék és por eltávolítására, megakadályozva, hogy a maradványok befolyásolják a későbbi folyamatokat vagy a forgács elektromos teljesítményét. - A nagy tisztaságú desztillált víz megakadályozza az új szennyeződések bejutását, így tiszta ostyakörnyezetet biztosít. |
Ellenőrzési fázis | -Optikai ellenőrzésOptikai érzékelő rendszerek és mesterséges intelligencia algoritmusok kombinációjával gyorsan azonosíthatók a hibák, biztosítva, hogy ne legyenek repedések vagy lepattanások a darabolt forgácsokban, javítva az ellenőrzés hatékonyságát és csökkentve az emberi hibákat. -Méretmérés: Ellenőrizze, hogy a chip méretei megfelelnek-e a tervezési specifikációknak. -Elektromos teljesítményvizsgálatBiztosítsa, hogy a kritikus chipek elektromos teljesítménye megfeleljen a szabványoknak, garantálva a megbízhatóságot a későbbi alkalmazásokban. |
Rendezési fázis | - Robotkarok vagy vákuumos tapadókorongok segítségével válassza le a minősített chipeket a szalagkeretről, és automatikusan rendezze azokat teljesítményük alapján, biztosítva a termelési hatékonyságot és rugalmasságot, miközben javítja a pontosságot. |
A szeletvágási folyamat magában foglalja a szelet tisztítását, pozicionálását, vágását, tisztítását, ellenőrzését és válogatását, ahol minden lépés kritikus fontosságú. Az automatizálás, a lézervágás és a mesterséges intelligencia által vezérelt ellenőrzési technológiák fejlődésével a modern szeletvágó rendszerek nagyobb pontosságot, sebességet és alacsonyabb anyagveszteséget érhetnek el. A jövőben az új vágási technológiák, mint például a lézer és a plazma, fokozatosan felváltják a hagyományos pengéjű vágást, hogy megfeleljenek az egyre összetettebb chiptervezés igényeinek, tovább ösztönözve a félvezető gyártási folyamatok fejlődését.
Ostyavágási technológia és alapelvei
A kép három elterjedt ostyavágási technológiát szemléltet:Penge aprítás,Lézeres kockázás, ésPlazma kockázásAz alábbiakban részletes elemzést és kiegészítő magyarázatot talál e három technikáról:
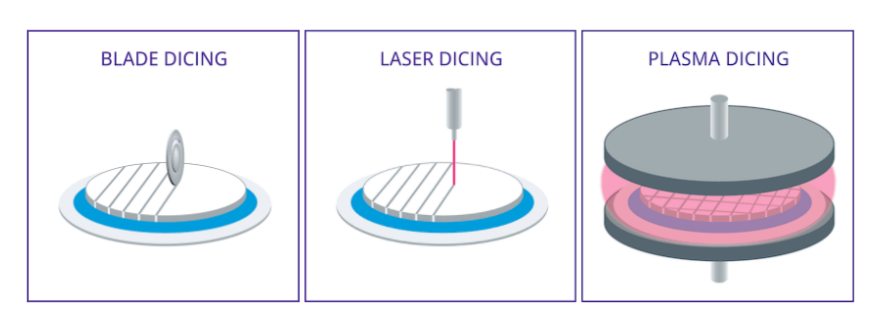
A félvezetőgyártásban a lapkavágás kulcsfontosságú lépés, amelyhez a lapka vastagsága alapján kell kiválasztani a megfelelő vágási módszert. Az első lépés a lapka vastagságának meghatározása. Ha a lapka vastagsága meghaladja a 100 mikront, akkor a pengés vágás választható vágási módszerként. Ha a pengés vágás nem megfelelő, akkor a töréses vágási módszer alkalmazható, amely magában foglalja mind a karcolásos vágást, mind a pengés vágási technikákat.
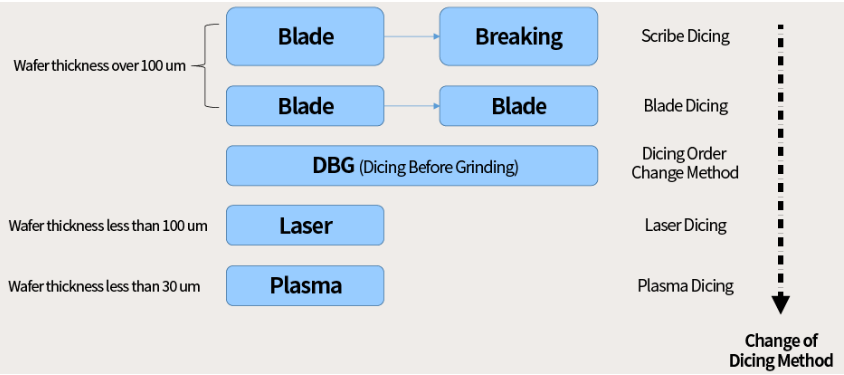
Amikor a lapka vastagsága 30 és 100 mikron között van, a DBG (Dice Before Grinding, azaz kockázás őrlés előtt) módszer ajánlott. Ebben az esetben a legjobb eredmény elérése érdekében karcolás, pengés kockázás vagy a vágási sorrend szükség szerinti módosítása választható.
A 30 mikronnál vékonyabb ultravékony ostyák esetében a lézervágás az előnyben részesített módszer, mivel képes a vékony ostyák precíz vágására anélkül, hogy túlzott kárt okozna. Ha a lézervágás nem képes megfelelni a speciális követelményeknek, alternatívaként plazmavágás is alkalmazható. Ez a folyamatábra egyértelmű döntéshozatali utat biztosít annak biztosítására, hogy a különböző vastagsági feltételek mellett a legmegfelelőbb ostyavágási technológia kerüljön kiválasztásra.
2.1 Mechanikus forgácsolási technológia
A mechanikus vágási technológia a hagyományos módszer az ostya kockázásában. Az alapelv egy nagy sebességű forgó gyémántcsiszolókorong használata vágószerszámként az ostya szeleteléséhez. A fő berendezések közé tartozik egy légcsapágyas orsó, amely nagy sebességgel hajtja a gyémántcsiszolókorongot, hogy precíz vágást vagy hornyolást végezzen egy előre meghatározott vágási útvonal mentén. Ez a technológia széles körben elterjedt az iparban az alacsony költség, a magas hatékonyság és a széleskörű alkalmazhatóság miatt.
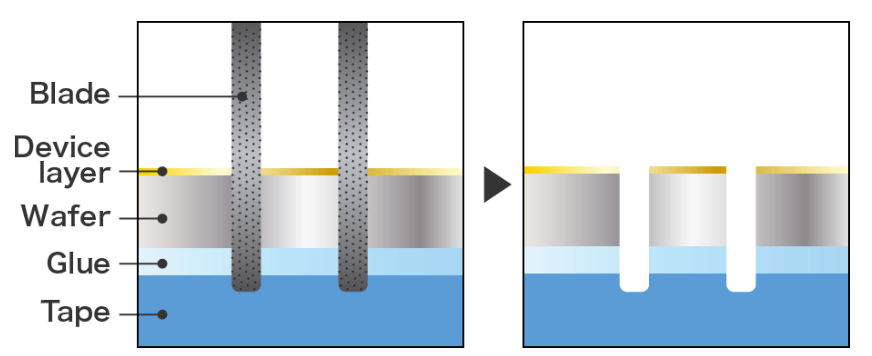
Előnyök
A gyémántcsiszolókorongok nagy keménysége és kopásállósága lehetővé teszi a mechanikus forgácsolótechnológia számára, hogy alkalmazkodjon a különféle szeletanyagok vágási igényeihez, legyenek azok hagyományos szilícium alapú anyagok vagy újabb összetett félvezetők. Működése egyszerű, viszonylag alacsony műszaki követelményekkel jár, ami tovább növeli népszerűségét a tömegtermelésben. Ezenkívül a lézervágáshoz hasonló más vágási módszerekhez képest a mechanikus forgácsolás költséghatékonyabb, így alkalmassá teszi nagy volumenű gyártási igények kielégítésére.
Korlátozások
Számos előnye ellenére a mechanikus forgácsolási technológiának vannak korlátai is. Először is, a szerszám és a lapka közötti fizikai érintkezés miatt a vágási pontosság viszonylag korlátozott, ami gyakran méretbeli eltérésekhez vezet, amelyek befolyásolhatják a későbbi chipcsomagolás és -tesztelés pontosságát. Másodszor, a mechanikus forgácsolási folyamat során könnyen előfordulhatnak olyan hibák, mint a lepattogzás és a repedések, ami nemcsak a hozamot befolyásolja, hanem negatívan befolyásolhatja a chipek megbízhatóságát és élettartamát is. A mechanikai feszültség okozta károsodás különösen káros a nagy sűrűségű chipgyártásnál, különösen törékeny anyagok forgácsolásakor, ahol ezek a problémák hangsúlyosabbak.
Technológiai fejlesztések
Ezen korlátozások leküzdésére a kutatók folyamatosan optimalizálják a mechanikus forgácsolási folyamatot. A legfontosabb fejlesztések közé tartozik a köszörűkorongok kialakításának és anyagválasztásának javítása a vágási pontosság és tartósság javítása érdekében. Ezenkívül a vágóberendezések szerkezeti kialakításának és vezérlőrendszereinek optimalizálása tovább javította a forgácsolási folyamat stabilitását és automatizálását. Ezek a fejlesztések csökkentik az emberi műveletek által okozott hibákat, és javítják a vágások következetességét. A fejlett ellenőrzési és minőségellenőrzési technológiák bevezetése a forgácsolási folyamat során fellépő rendellenességek valós idejű monitorozására szintén jelentősen javította a vágás megbízhatóságát és hozamát.
Jövőbeli fejlődés és új technológiák
Bár a mechanikus forgácsolási technológia továbbra is jelentős helyet foglal el a szeletvágásban, az új forgácsolási technológiák gyorsan fejlődnek a félvezető-feldolgozási folyamatok fejlődésével. Például a termikus lézervágási technológia alkalmazása új megoldásokat kínál a mechanikus forgácsolás pontossági és hibaproblémáira. Ez az érintésmentes forgácsolási módszer csökkenti a szelet fizikai igénybevételét, jelentősen mérsékelve a lepattogzás és a repedés előfordulását, különösen a törékenyebb anyagok vágása esetén. A jövőben a mechanikus forgácsolási technológia és az új forgácsolási technikák integrációja több lehetőséget és rugalmasságot biztosít a félvezetőgyártás számára, tovább javítva a gyártási hatékonyságot és a chipek minőségét.
Összefoglalva, bár a mechanikus forgácsolási technológiának vannak bizonyos hátrányai, a folyamatos technológiai fejlesztések és az új forgácsolási technikákkal való integrációja lehetővé teszi, hogy továbbra is fontos szerepet játsszon a félvezetőgyártásban, és megőrizze versenyképességét a jövőbeli folyamatokban.
2.2 Lézervágási technológia
A lézervágási technológia, mint a szeletvágás új módszere, fokozatosan széles körű figyelmet kapott a félvezetőiparban nagy pontossága, a mechanikai érintkezési sérülések hiánya és a gyors vágási képességek miatt. Ez a technológia a lézersugár nagy energiasűrűségét és fókuszáló képességét használja ki, hogy egy kis hőhatásövezetet hozzon létre a szelet anyagának felületén. Amikor a lézersugarat a szeletre alkalmazzák, a keletkező hőfeszültség az anyag kijelölt helyen történő repedését okozza, így precíz vágást ér el.
A lézervágási technológia előnyei
• Nagy pontosságA lézersugár precíz pozicionálási képessége mikron- vagy akár nanométeres szintű vágási pontosságot tesz lehetővé, megfelelve a modern nagy pontosságú, nagy sűrűségű integrált áramköri gyártás követelményeinek.
• Nincs mechanikus érintkezésA lézervágás elkerüli a lapkával való fizikai érintkezést, megakadályozva a mechanikus vágás során gyakran előforduló problémákat, például a lepattogzást és a repedést, jelentősen javítva a chipek hozamát és megbízhatóságát.
• Gyors vágási sebességA lézervágás nagy sebessége hozzájárul a megnövekedett termelési hatékonysághoz, így különösen alkalmas nagyméretű, nagy sebességű gyártási forgatókönyvekhez.
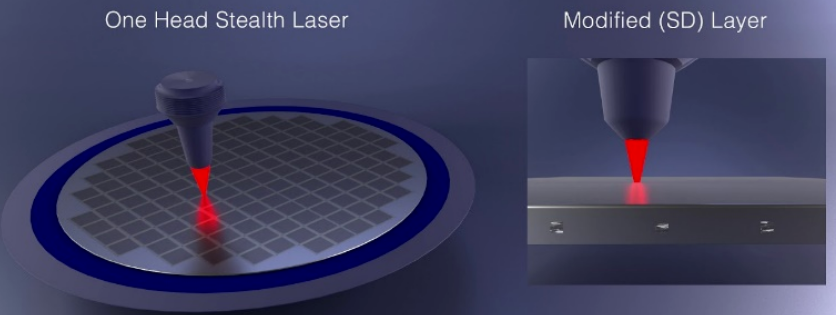
Kihívások
• Magas felszerelési költségekA lézervágó berendezések kezdeti beruházási költsége magas, ami gazdasági nyomást jelent, különösen a kis- és középvállalkozások számára.
• Komplex folyamatirányításA lézervágás számos paraméter pontos szabályozását igényli, beleértve az energiasűrűséget, a fókuszpozíciót és a vágási sebességet, ami összetetté teszi a folyamatot.
• Hőhatásnak kitett zónákkal kapcsolatos problémákBár a lézervágás érintésmentes jellege csökkenti a mechanikai sérüléseket, a hőhatásövezet (HAZ) által okozott hőfeszültség negatívan befolyásolhatja a lapka anyagának tulajdonságait. A folyamat további optimalizálása szükséges ennek a hatásnak a minimalizálása érdekében.
Technológiai fejlesztési irányok
Ezen kihívások megoldása érdekében a kutatók a berendezések költségeinek csökkentésére, a vágási hatékonyság javítására és a folyamatok optimalizálására összpontosítanak.
• Hatékony lézerek és optikai rendszerekHatékonyabb lézerek és fejlettebb optikai rendszerek fejlesztésével csökkenthetők a berendezések költségei, miközben javul a vágási pontosság és sebesség.
• Folyamatparaméterek optimalizálásaA lézerek és a lapkaanyagok közötti kölcsönhatás mélyreható kutatása folyamatban van a hőhatásövezetet csökkentő eljárások fejlesztése érdekében, ezáltal javítva a vágási minőséget.
• Intelligens vezérlőrendszerekAz intelligens vezérlési technológiák fejlesztésének célja a lézervágási folyamat automatizálása és optimalizálása, stabilitásának és konzisztenciájának javítása.
A lézervágási technológia különösen hatékony az ultravékony ostyák és a nagy pontosságú vágási forgatókönyvek esetében. Ahogy a ostyák mérete és az áramköri sűrűség növekszik, a hagyományos mechanikus vágási módszerek egyre nehezebben tudják kielégíteni a modern félvezetőgyártás nagy pontosságú és nagy hatékonyságú követelményeit. Egyedi előnyei miatt a lézervágás egyre inkább az előnyben részesített megoldássá válik ezeken a területeken.
Bár a lézervágási technológia továbbra is olyan kihívásokkal néz szembe, mint a magas berendezésköltségek és a folyamatok összetettsége, a nagy pontosság és az érintésmentes károsodás egyedülálló előnyei fontos fejlesztési irányt jelentenek a félvezetőgyártásban. Ahogy a lézertechnológia és az intelligens vezérlőrendszerek folyamatosan fejlődnek, a lézervágás várhatóan tovább javítja a lapkavágás hatékonyságát és minőségét, ami a félvezetőipar folyamatos fejlődésének motorja.
2.3 Plazmavágási technológia
A plazmavágási technológia, mint egy feltörekvő szeletvágási módszer, az utóbbi években jelentős figyelmet kapott. Ez a technológia nagy energiájú plazmasugarakat használ a szeletek precíz vágására a plazmasugár energiájának, sebességének és vágási útvonalának szabályozásával, optimális vágási eredményeket érve el.
Működési elv és előnyök
A plazmavágás folyamata a berendezés által generált magas hőmérsékletű, nagy energiájú plazmasugáron alapul. Ez a sugár nagyon rövid idő alatt képes felmelegíteni a lapka anyagát olvadáspontjára vagy párolgáspontjára, lehetővé téve a gyors vágást. A hagyományos mechanikus vagy lézeres vágáshoz képest a plazmavágás gyorsabb és kisebb hőhatásövezetet hoz létre, így hatékonyan csökkenti a repedések és sérülések előfordulását a vágás során.
A gyakorlati alkalmazásokban a plazmavágási technológia különösen alkalmas összetett alakú szeletek kezelésére. Nagy energiájú, állítható plazmasugara könnyedén és nagy pontossággal vághat szabálytalan alakú szeleteket. Ezért a mikroelektronikai gyártásban, különösen a csúcskategóriás chipek egyedi és kis tételben történő gyártásában, ez a technológia nagy ígéretet mutat a széles körű elterjedés szempontjából.
Kihívások és korlátok
A plazmavágási technológia számos előnye ellenére bizonyos kihívásokkal is szembesül.
• Komplex folyamatA plazmavágási folyamat összetett, és nagy pontosságú berendezéseket, valamint tapasztalt kezelőket igényel a biztosításához.pontosság és stabilitás a vágásban.
• Környezetvédelmi ellenőrzés és biztonságA plazmasugár magas hőmérsékletű és nagy energiájú jellege szigorú környezeti ellenőrzést és biztonsági intézkedéseket igényel, ami növeli a megvalósítás bonyolultságát és költségeit.
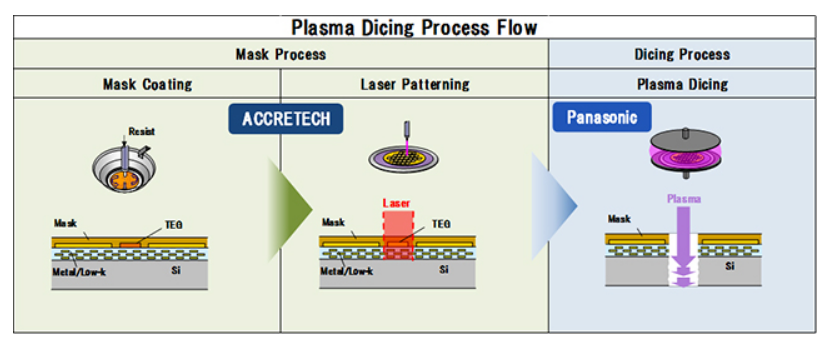
Jövőbeli fejlesztési irányok
A technológiai fejlődéssel várhatóan fokozatosan leküzdhetők a plazmavágással kapcsolatos kihívások. Intelligensebb és stabilabb vágóberendezések fejlesztésével csökkenthető a kézi műveletektől való függőség, ezáltal javítható a termelési hatékonyság. Ugyanakkor a folyamatparaméterek és a vágási környezet optimalizálása segít csökkenteni a biztonsági kockázatokat és az üzemeltetési költségeket.
A félvezetőiparban a szeletvágási és -kockázási technológia innovációi kulcsfontosságúak az iparág fejlődésének előmozdítása szempontjából. A plazmavágási technológia, nagy pontosságával, hatékonyságával és összetett szeletformák kezelésének képességével, jelentős új szereplővé vált ezen a területen. Bár továbbra is fennállnak kihívások, ezeket a problémákat fokozatosan fogják kezelni a folyamatos technológiai innovációk, amelyek több lehetőséget és esélyt teremtenek a félvezetőgyártás számára.
A plazmavágási technológia alkalmazási lehetőségei hatalmasak, és a jövőben várhatóan egyre fontosabb szerepet fog játszani a félvezetőgyártásban. A folyamatos technológiai innováció és optimalizálás révén a plazmavágás nemcsak a meglévő kihívásokat fogja megoldani, hanem a félvezetőipar növekedésének erőteljes hajtóerejévé is válik.
2.4 Forgácsolási minőség és befolyásoló tényezők
A szeletvágás minősége kritikus fontosságú a későbbi chipcsomagolás, tesztelés, valamint a végtermék általános teljesítménye és megbízhatósága szempontjából. A vágás során gyakran előforduló problémák közé tartoznak a repedések, a lepattogzás és a vágási eltérések. Ezeket a problémákat számos tényező együttes hatása befolyásolja.
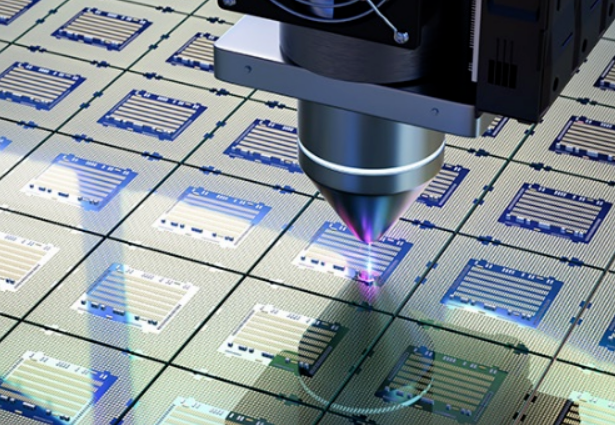
Kategória | Tartalom | Hatás |
Folyamatparaméterek | A forgácsolási sebesség, az előtolási sebesség és a forgácsolási mélység közvetlenül befolyásolja a forgácsolási folyamat stabilitását és pontosságát. A nem megfelelő beállítások feszültségkoncentrációhoz és túlzott hőhatásövezethez vezethetnek, ami repedéseket és lepattogzást eredményez. A paraméterek megfelelő beállítása a lapka anyaga, vastagsága és a forgácsolási követelmények alapján kulcsfontosságú a kívánt vágási eredmények eléréséhez. | A megfelelő folyamatparaméterek biztosítják a precíz vágást és csökkentik a repedések és lepattogzások kockázatát. |
Berendezések és anyagi tényezők | -Penge minőségeA penge anyaga, keménysége és kopásállósága befolyásolja a vágási folyamat simaságát és a vágott felület síkságát. A rossz minőségű pengék növelik a súrlódást és a hőfeszültséget, ami repedésekhez vagy lepattogzáshoz vezethet. A megfelelő pengeanyag kiválasztása kulcsfontosságú. -Hűtőfolyadék teljesítményeA hűtőfolyadékok segítenek csökkenteni a forgácsolási hőmérsékletet, minimalizálni a súrlódást és eltávolítani a törmeléket. A nem hatékony hűtőfolyadék magas hőmérsékletet és törmeléklerakódást okozhat, ami befolyásolhatja a vágás minőségét és hatékonyságát. A hatékony és környezetbarát hűtőfolyadékok kiválasztása létfontosságú. | A penge minősége befolyásolja a vágás pontosságát és simaságát. A nem hatékony hűtőfolyadék gyenge vágási minőséget és hatékonyságot eredményezhet, ami kiemeli az optimális hűtőfolyadék-felhasználás szükségességét. |
Folyamatszabályozás és minőségellenőrzés | -FolyamatszabályozásA kulcsfontosságú vágási paraméterek valós idejű monitorozása és beállítása a vágási folyamat stabilitásának és következetességének biztosítása érdekében. -MinőségellenőrzésA vágás utáni megjelenési ellenőrzések, méretmérések és elektromos teljesítménytesztek segítenek a minőségi problémák gyors azonosításában és kezelésében, javítva a vágási pontosságot és az állandóságot. | A megfelelő folyamatirányítás és minőségellenőrzés segít biztosítani az állandó, kiváló minőségű vágási eredményeket és a potenciális problémák korai felismerését. |

A vágási minőség javítása
A vágási minőség javítása átfogó megközelítést igényel, amely figyelembe veszi a folyamatparamétereket, a berendezések és anyagok kiválasztását, a folyamatirányítást és az ellenőrzést. A vágási technológiák folyamatos finomításával és a folyamatmódszerek optimalizálásával tovább javítható a szeletvágás pontossága és stabilitása, megbízhatóbb műszaki támogatást nyújtva a félvezetőgyártó ipar számára.
#03 Vágás utáni kezelés és tesztelés
3.1 Tisztítás és szárítás
A wafer vágás utáni tisztítási és szárítási lépések kritikus fontosságúak a chip minőségének és a későbbi folyamatok zökkenőmentes lebonyolításának biztosítása érdekében. Ebben a szakaszban elengedhetetlen a szilíciumtörmelék, a hűtőfolyadék-maradványok és a vágás során keletkező egyéb szennyeződések alapos eltávolítása. Ugyanilyen fontos biztosítani, hogy a chipek ne sérüljenek meg a tisztítási folyamat során, és szárítás után ügyelni kell arra, hogy ne maradjon nedvesség a chip felületén, hogy elkerüljük az olyan problémákat, mint a korrózió vagy az elektrosztatikus kisülés.
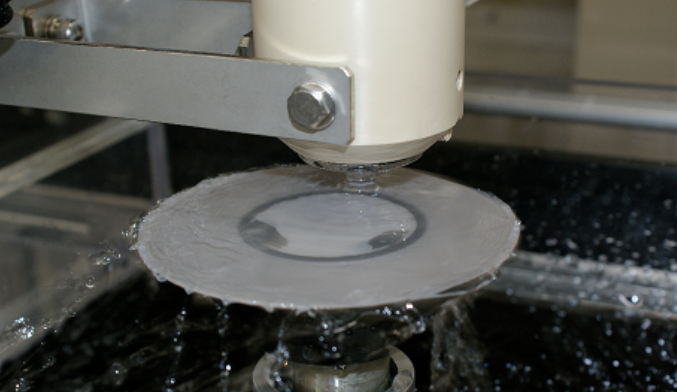
Vágás utáni kezelés: Tisztítási és szárítási folyamat
Folyamatlépés | Tartalom | Hatás |
Tisztítási folyamat | -MódszerHasználjon speciális tisztítószereket és tiszta vizet, ultrahangos vagy mechanikus kefés tisztítással kombinálva. | Biztosítja a szennyeződések alapos eltávolítását és megakadályozza a forgácsok károsodását tisztítás közben. |
-Tisztítószer kiválasztásaA hatékony tisztítás érdekében a chip károsodása nélkül válasszon a lapka anyaga és a szennyeződés típusa alapján. | A megfelelő tisztítószer kiválasztása kulcsfontosságú a hatékony tisztításhoz és a vágások elleni védelemhez. | |
-ParamétervezérlésSzigorúan ellenőrizze a tisztítási hőmérsékletet, időt és a tisztítóoldat koncentrációját, hogy elkerülje a nem megfelelő tisztítás okozta minőségi problémákat. | A szabályozások segítenek elkerülni az ostya károsodását vagy a szennyeződések visszamaradását, biztosítva az állandó minőséget. | |
Szárítási folyamat | -Hagyományos módszerekTermészetes levegős szárítás és forró levegős szárítás, amelyek alacsony hatásfokúak és statikus elektromosság felhalmozódásához vezethetnek. | Lassabb száradási időt és statikus elektromos problémákat okozhat. |
-Modern technológiákHasználjon fejlett technológiákat, például vákuumszárítást és infravörös szárítást a forgácsok gyors száradása és a káros hatások elkerülése érdekében. | Gyorsabb és hatékonyabb szárítási folyamat, csökkentve a sztatikus kisülés vagy a nedvességgel kapcsolatos problémák kockázatát. | |
Berendezések kiválasztása és karbantartása | -Felszerelés kiválasztásaA nagy teljesítményű tisztító- és szárítógépek javítják a feldolgozási hatékonyságot, és finoman szabályozzák a kezelés során felmerülő esetleges problémákat. | A kiváló minőségű gépek jobb feldolgozást biztosítanak, és csökkentik a tisztítás és szárítás során előforduló hibák valószínűségét. |
-Berendezések karbantartásaA berendezések rendszeres ellenőrzése és karbantartása biztosítja azok optimális üzemállapotát, garantálva a forgács minőségét. | A megfelelő karbantartás megakadályozza a berendezések meghibásodását, biztosítva a megbízható és kiváló minőségű feldolgozást. |
Vágás utáni tisztítás és szárítás
A lapkavágás utáni tisztítási és szárítási lépések összetett és kényes folyamatok, amelyek több tényező gondos figyelembevételét igénylik a végeredmény biztosítása érdekében. Tudományos módszerek és szigorú eljárások alkalmazásával biztosítható, hogy minden egyes chip optimális állapotban kerüljön a következő csomagolási és tesztelési szakaszokba.
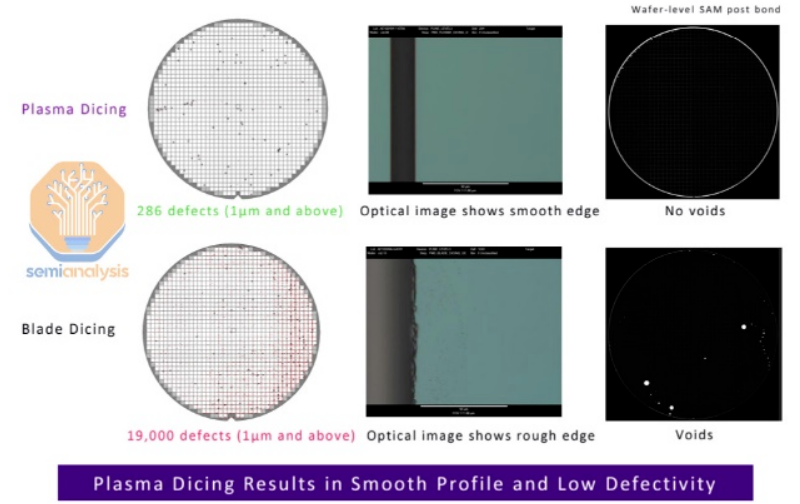
Vágás utáni ellenőrzés és tesztelés
Lépés | Tartalom | Hatás |
Ellenőrzési lépés | 1.Vizuális ellenőrzésVizuális vagy automatizált ellenőrző berendezésekkel ellenőrizze a chip felületén látható hibákat, például repedéseket, lepattogzást vagy szennyeződéseket. A fizikailag sérült chipek gyors azonosítása a hulladék elkerülése érdekében. | Segít a hibás forgácsok korai azonosításában és kiküszöbölésében, csökkentve az anyagveszteséget. |
2.MéretmérésHasználjon precíziós mérőeszközöket a forgács méreteinek pontos méréséhez, biztosítva, hogy a vágási méret megfeleljen a tervezési specifikációknak, és megelőzve a teljesítményproblémákat vagy a csomagolási nehézségeket. | Biztosítja, hogy a chipek a kívánt méretkorlátokon belül legyenek, megakadályozva a teljesítményromlást vagy az összeszerelési problémákat. | |
3.Elektromos teljesítményvizsgálatÉrtékelje a kulcsfontosságú elektromos paramétereket, például az ellenállást, a kapacitást és az induktivitást, hogy azonosítsa a nem megfelelő chipeket, és biztosítsa, hogy csak a teljesítményminősítésű chipek lépjenek tovább a következő szakaszba. | Biztosítja, hogy csak működőképes és teljesítménytesztelt chipek kerüljenek tovább a folyamatban, csökkentve a későbbi szakaszokban a meghibásodás kockázatát. | |
Tesztelési lépés | 1.Funkcionális tesztelés: Ellenőrizze, hogy a chip alapvető funkciói a tervek szerint működnek-e, azonosítva és kiküszöbölve a funkcionális rendellenességeket mutató chipeket. | Biztosítja, hogy a chipek megfeleljenek az alapvető működési követelményeknek, mielőtt a későbbi szakaszokba lépnének. |
2.Megbízhatósági tesztelés: A chip teljesítménystabilitásának értékelése hosszan tartó használat vagy zord környezeti körülmények között, jellemzően magas hőmérsékletű öregítéssel, alacsony hőmérsékletű teszteléssel és páratartalom-teszteléssel a valós szélsőséges körülmények szimulálására. | Biztosítja a chipek megbízható működését különféle környezeti feltételek mellett, javítva a termék élettartamát és stabilitását. | |
3.Kompatibilitási tesztelés: Ellenőrizze, hogy a chip megfelelően működik-e más alkatrészekkel vagy rendszerekkel, ügyelve arra, hogy ne legyenek hibák vagy teljesítményromlás az inkompatibilitás miatt. | Biztosítja a zökkenőmentes működést a valós alkalmazásokban a kompatibilitási problémák megelőzésével. |
3.3 Csomagolás és tárolás
A szeletvágás után a chipek a félvezetőgyártási folyamat kulcsfontosságú termékei, csomagolási és tárolási szakaszaik pedig ugyanilyen fontosak. A megfelelő csomagolási és tárolási intézkedések nemcsak a chipek szállítás és tárolás közbeni biztonságának és stabilitásának biztosításához elengedhetetlenek, hanem a későbbi gyártási, tesztelési és csomagolási szakaszok szilárd alátámasztásához is.
Az ellenőrzési és tesztelési szakaszok összefoglalása:
A lapkavágás utáni chipek ellenőrzési és tesztelési lépései számos aspektust felölelnek, beleértve a vizuális ellenőrzést, a méretmérést, az elektromos teljesítménytesztet, a funkcionális tesztelést, a megbízhatósági tesztelést és a kompatibilitási tesztelést. Ezek a lépések összefüggenek és kiegészítik egymást, szilárd akadályt képezve a termékminőség és megbízhatóság biztosítása érdekében. Szigorú ellenőrzési és tesztelési eljárások révén a potenciális problémák azonnal azonosíthatók és megoldhatók, biztosítva, hogy a végtermék megfeleljen az ügyfél követelményeinek és elvárásainak.
Vonatkozás | Tartalom |
Csomagolási intézkedések | 1.AntisztatikusA csomagolóanyagoknak kiváló antisztatikus tulajdonságokkal kell rendelkezniük, hogy megakadályozzák a sztatikus elektromosság okozta károsodást az eszközökben vagy azok teljesítményének romlását. |
2.NedvességállóA csomagolóanyagoknak jó nedvességállósággal kell rendelkezniük, hogy megakadályozzák a korróziót és az elektromos teljesítmény páratartalom okozta romlását. | |
3.ÜtésállóA csomagolóanyagoknak hatékony ütéscsillapítást kell biztosítaniuk, hogy megvédjék a chipeket a rezgéstől és az ütésektől szállítás közben. | |
Tárolási környezet | 1.Páratartalom-szabályozás: Szigorúan szabályozza a páratartalmat a megfelelő tartományon belül, hogy megakadályozza a nedvesség felszívódását és a túlzott páratartalom okozta korróziót, illetve az alacsony páratartalom okozta statikus problémákat. |
2.Tisztaság: Tartson fenn tiszta tárolási környezetet, hogy elkerülje a forgácsok porral és szennyeződésekkel való szennyeződését. | |
3.Hőmérséklet-szabályozás: Állítson be egy ésszerű hőmérsékleti tartományt, és tartsa fenn a hőmérséklet stabilitását, hogy megakadályozza a túlzott hő vagy az alacsony hőmérséklet okozta páralecsapódási problémák miatti gyorsított öregedést. | |
Rendszeres ellenőrzés | Rendszeresen ellenőrizze és értékelje a tárolt chipeket vizuális ellenőrzések, méretmérések és elektromos teljesítménytesztek segítségével, hogy időben azonosítsa és kezelje a lehetséges problémákat. A tárolási idő és körülmények alapján tervezze meg a chipek felhasználását, hogy azok optimális állapotban legyenek felhasználva. |
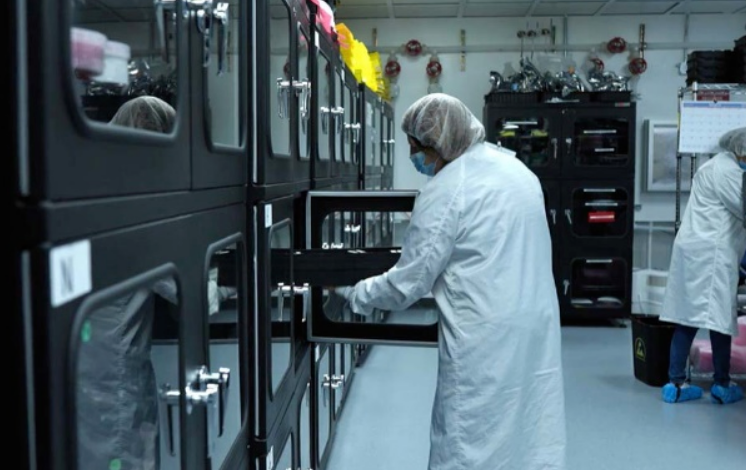
A félvezetőgyártásban jelentős kihívást jelentenek a mikrorepedések és sérülések a wafer kockázási folyamata során. A forgácsolási feszültség a jelenség elsődleges oka, mivel apró repedéseket és sérüléseket okoz a wafer felületén, ami a gyártási költségek növekedéséhez és a termékminőség romlásához vezet.
Ennek a kihívásnak a megoldása érdekében kulcsfontosságú a forgácsolási feszültség minimalizálása, valamint az optimalizált forgácsolási technikák, szerszámok és feltételek alkalmazása. Az olyan tényezőkre való gondos odafigyelés, mint a penge anyaga, a forgácsolási sebesség, a nyomás és a hűtési módszerek, segíthet csökkenteni a mikrorepedések kialakulását és javítani a folyamat összhozamát. Ezenkívül a fejlettebb vágási technológiákkal, például a lézeres forgácsolással kapcsolatos folyamatos kutatások a problémák további enyhítésének módjait vizsgálják.
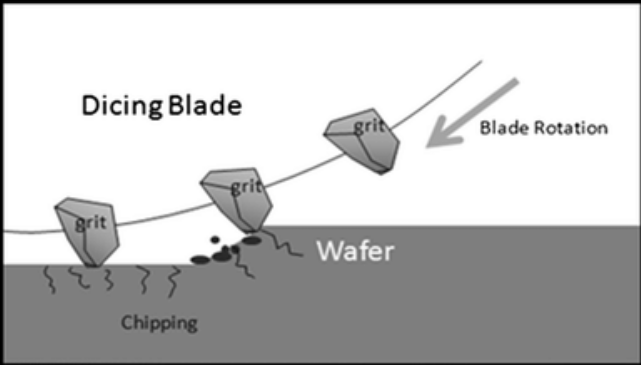
Törékeny anyagként a lapkák hajlamosak belső szerkezeti változásokra mechanikai, termikus vagy kémiai igénybevétel hatására, ami mikrorepedések kialakulásához vezet. Bár ezek a repedések nem feltétlenül azonnal észrevehetők, a gyártási folyamat előrehaladtával kitágulhatnak és súlyosabb károkat okozhatnak. Ez a probléma különösen a későbbi csomagolási és tesztelési szakaszokban válik problematikussá, ahol a hőmérséklet-ingadozások és a további mechanikai igénybevételek miatt ezek a mikrorepedések látható törésekké alakulhatnak, ami potenciálisan chiphibához vezethet.
A kockázat csökkentése érdekében elengedhetetlen a vágási folyamat gondos szabályozása olyan paraméterek optimalizálásával, mint a vágási sebesség, a nyomás és a hőmérséklet. A kevésbé agresszív vágási módszerek, például a lézeres darabolás, csökkenthetik a lapka mechanikai igénybevételét és minimalizálhatják a mikrorepedések kialakulását. Ezenkívül a fejlett vizsgálati módszerek, mint az infravörös szkennelés vagy a röntgenképalkotás alkalmazása a lapka darabolási folyamata során segíthet a korai stádiumú repedések észlelésében, mielőtt további károkat okoznának.
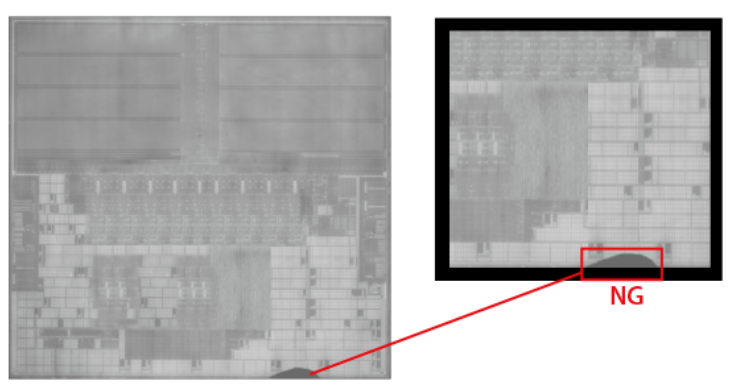
A lapka felületének sérülése jelentős aggodalomra ad okot a szeletelési folyamat során, mivel közvetlen hatással lehet a chip teljesítményére és megbízhatóságára. Az ilyen károkat okozhatja a vágószerszámok nem megfelelő használata, a helytelen vágási paraméterek vagy magában a lapkában rejlő anyaghibák. Az októl függetlenül ezek a sérülések az áramkör elektromos ellenállásának vagy kapacitásának megváltozásához vezethetnek, ami befolyásolja az általános teljesítményt.
Ezen problémák megoldására két fő stratégiát vizsgálnak:
1. Forgácsolószerszámok és paraméterek optimalizálásaÉlesebb pengék használatával, a vágási sebesség beállításával és a vágási mélység módosításával minimalizálható a feszültségkoncentráció a vágási folyamat során, ezáltal csökkentve a károsodás lehetőségét.
2. Új vágási technológiák feltárásaA fejlett technikák, mint például a lézervágás és a plazmavágás, nagyobb pontosságot kínálnak, miközben potenciálisan csökkentik a lapkát érő károsodás mértékét. Ezeket a technológiákat tanulmányozzák, hogy megtalálják a módját a nagy vágási pontosság elérésének, miközben minimalizálják a lapka termikus és mechanikai igénybevételét.
Termikus hatásterület és annak hatása a teljesítményre
A lézer- és plazmavágáshoz hasonló termikus vágási eljárások során a magas hőmérséklet elkerülhetetlenül hőhatászónát hoz létre a lapka felületén. Ez a terület, ahol a hőmérséklet-gradiens jelentős, megváltoztathatja az anyag tulajdonságait, és ezáltal befolyásolhatja a chip végső teljesítményét.
A termikus hatásövezet (TAZ) hatása:
Kristályszerkezeti változásokMagas hőmérsékleten a lapkaanyag atomjai átrendeződhetnek, ami torzulásokat okozhat a kristályszerkezetben. Ez a torzulás gyengíti az anyagot, csökkenti mechanikai szilárdságát és stabilitását, ami növeli a chip meghibásodásának kockázatát használat közben.
Az elektromos tulajdonságok változásaiA magas hőmérséklet megváltoztathatja a töltéshordozók koncentrációját és mobilitását a félvezető anyagokban, ami hatással van a chip elektromos vezetőképességére és áramátviteli hatékonyságára. Ezek a változások a chip teljesítményének romlásához vezethetnek, ami potenciálisan alkalmatlanná teheti a rendeltetésének megfelelő működésre.
Ezen hatások enyhítése érdekében a forgácsolás során a hőmérséklet szabályozása, a forgácsolási paraméterek optimalizálása, valamint olyan módszerek feltárása, mint a hűtőfúvókák vagy az utófeldolgozási kezelések, alapvető fontosságú stratégiák a hőhatás mértékének csökkentése és az anyag integritásának megőrzése érdekében.
Összességében mind a mikrorepedések, mind a hőhatászónák kulcsfontosságú kihívást jelentenek a wafer kockázási technológiájában. A félvezető termékek minőségének javítása és piaci versenyképességének fokozása érdekében folyamatos kutatásra lesz szükség a technológiai fejlesztések és a minőségellenőrzési intézkedések mellett.
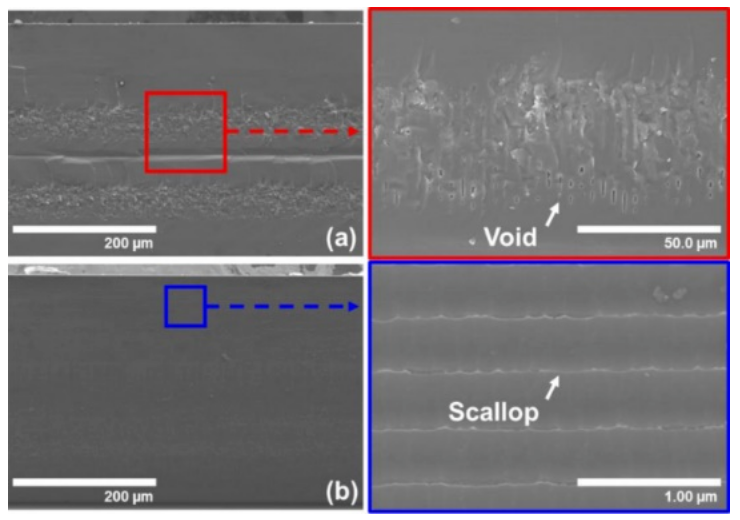
A termikus hatásterület szabályozására szolgáló intézkedések:
Forgácsolási folyamatparaméterek optimalizálásaA vágási sebesség és teljesítmény csökkentése hatékonyan minimalizálhatja a termikus ütközési zóna (TAZ) méretét. Ez segít szabályozni a vágási folyamat során keletkező hő mennyiségét, ami közvetlenül befolyásolja a lapka anyagtulajdonságait.
Fejlett hűtési technológiákAz olyan technológiák alkalmazása, mint a folyékony nitrogénes hűtés és a mikrofluidikus hűtés, jelentősen korlátozhatja a termikus ütközési zóna tartományát. Ezek a hűtési módszerek hatékonyabban vezetik el a hőt, ezáltal megőrizve az ostya anyagtulajdonságait és minimalizálva a hőkárosodást.
AnyagválasztásA kutatók új anyagokat, például szén nanocsöveket és grafént vizsgálnak, amelyek kiváló hővezető képességgel és mechanikai szilárdsággal rendelkeznek. Ezek az anyagok csökkenthetik a hőhatászónát, miközben javítják a chipek általános teljesítményét.
Összefoglalva, bár a termikus ütközési zóna a termikus vágási technológiák elkerülhetetlen következménye, optimalizált feldolgozási technikákkal és anyagválasztással hatékonyan szabályozható. A jövőbeli kutatások valószínűleg a termikus vágási folyamatok finomhangolására és automatizálására fognak összpontosítani a hatékonyabb és pontosabb szeletkockázás elérése érdekében.

Egyensúlystratégia:
Az ostyakihozatal és a termelési hatékonyság közötti optimális egyensúly elérése folyamatos kihívást jelent az ostyaaprítási technológiában. A gyártóknak számos tényezőt figyelembe kell venniük, például a piaci keresletet, a termelési költségeket és a termékminőséget, hogy racionális termelési stratégiát és folyamatparamétereket dolgozzanak ki. Ugyanakkor a fejlett vágóberendezések bevezetése, a kezelői készségek fejlesztése és az alapanyag-minőség-ellenőrzés fokozása elengedhetetlen a hozam fenntartásához vagy akár javításához, miközben növelik a termelési hatékonyságot.
Jövőbeli kihívások és lehetőségek:
A félvezető technológia fejlődésével a szeletvágás új kihívásokkal és lehetőségekkel néz szembe. Ahogy a chipméretek csökkennek és az integráció növekszik, a vágási pontossággal és minőséggel szembeni követelmények jelentősen megnőnek. Ezzel egyidejűleg az új technológiák új ötleteket kínálnak a szeletvágási technikák fejlesztéséhez. A gyártóknak lépést kell tartaniuk a piaci dinamikával és a technológiai trendekkel, folyamatosan módosítva és optimalizálva a termelési stratégiákat és a folyamatparamétereket, hogy megfeleljenek a piaci változásoknak és a technológiai igényeknek.
Összefoglalva, a piaci kereslet, a termelési költségek és a termékminőség szempontjainak integrálásával, valamint fejlett berendezések és technológiák bevezetésével, a kezelői készségek fejlesztésével és a nyersanyag-ellenőrzés megerősítésével a gyártók a legjobb egyensúlyt érhetik el a szelethozam és a termelési hatékonyság között a szeletkockázás során, ami hatékony és kiváló minőségű félvezető termékgyártáshoz vezet.
Jövőbeli kilátások:
A gyors technológiai fejlődésnek köszönhetően a félvezető technológia példátlan ütemben fejlődik. A félvezetőgyártás kritikus lépéseként a lapkavágási technológia izgalmas új fejlesztések előtt áll. A jövőben a lapkavágási technológia várhatóan jelentős javulást fog elérni a pontosság, a hatékonyság és a költségek terén, új lendületet adva a félvezetőipar folyamatos növekedésének.
A pontosság növelése:
A nagyobb pontosság elérése érdekében a lapkavágási technológia folyamatosan feszegeti a meglévő eljárások határait. A vágási folyamat fizikai és kémiai mechanizmusainak mélyreható tanulmányozásával és a vágási paraméterek pontos szabályozásával finomabb vágási eredményeket lehet elérni, hogy megfeleljenek az egyre összetettebb áramkör-tervezési követelményeknek. Ezenkívül az új anyagok és vágási módszerek feltárása jelentősen javítja a hozamot és a minőséget.
Hatékonyságnövelés:
Az új szeletvágó berendezések az intelligens és automatizált tervezésre fognak összpontosítani. A fejlett vezérlőrendszerek és algoritmusok bevezetése lehetővé teszi a berendezések számára, hogy automatikusan igazítsák a vágási paramétereket a különböző anyagokhoz és tervezési követelményekhez, ezáltal jelentősen javítva a termelési hatékonyságot. Az olyan innovációk, mint a többszeletes vágótechnológia és a gyors pengecsere-rendszerek, kulcsszerepet játszanak majd a hatékonyság növelésében.
Költségek csökkentése:
A költségek csökkentése kulcsfontosságú irány a lapkavágási technológia fejlesztésében. Az új anyagok és vágási módszerek fejlesztésével várhatóan a berendezések költségei és a karbantartási kiadások hatékonyan ellenőrizhetők lesznek. Ezenkívül a termelési folyamatok optimalizálása és a selejtarányok csökkentése tovább csökkenti a gyártás során keletkező hulladékot, ami az össztermelési költségek csökkenéséhez vezet.
Intelligens gyártás és IoT:
Az intelligens gyártás és a dolgok internetének (IoT) technológiáinak integrációja átalakuló változásokat hoz a lapkavágási technológiába. Az eszközök összekapcsolhatóságának és adatmegosztásának köszönhetően a gyártási folyamat minden lépése valós időben nyomon követhető és optimalizálható. Ez nemcsak a termelési hatékonyságot és a termékminőséget javítja, hanem pontosabb piaci előrejelzést és döntéshozatali támogatást is nyújt a vállalatoknak.
A jövőben a szeletvágási technológia figyelemre méltó előrelépéseket fog tenni a pontosság, a hatékonyság és a költségek terén. Ezek a fejlesztések előmozdítják a félvezetőipar folyamatos fejlődését, és további technológiai újításokat és kényelmet hoznak az emberi társadalom számára.
Közzététel ideje: 2024. november 19.